Achieve perfect OEE calculation with expert advice from industry professionals. This blog post reveals the key techniques and strategies for optimizing your operations. Read now to learn the secrets and take your efficiency to the next level!
Table of Contents
- Introduction: Unveiling the Secret Formula for Perfect OEE Calculation
- What is OEE and Why is it Important?
- The Foundation: Understanding the Components of OEE
- 1. Availability
- 2. Performance
- 3. Quality
- The Secret Formula for Perfect OEE Calculation
- SIMPLE OEE Calculation Steps
- Improving Your OEE – Practical Tips
- Common Pitfalls to Avoid in OEE Calculation
- Conclusion: Mastery Over OEE Calculation
- Call to Action
Introduction: Unveiling the Secret Formula for Perfect OEE Calculation
Have you ever wondered what the secret to perfect OEE calculation is? If you’re looking for a method to elevate your facility’s efficiency to new heights, you’re in the right place. This blog will guide you through everything you need to know about the Secret Formula for Perfect OEE Calculation Revealed! and the SIMPLE OEE Calculation method.
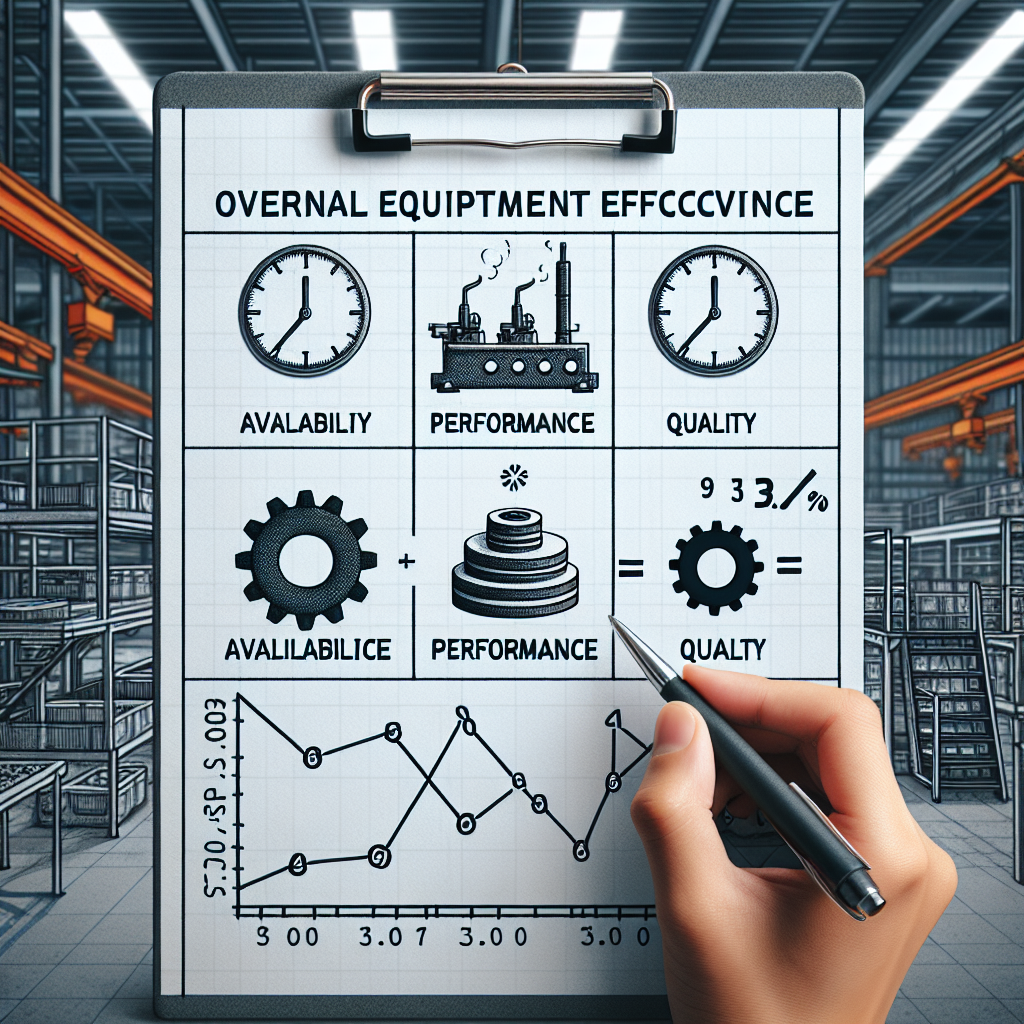
What is OEE and Why is it Important?
Overall Equipment Effectiveness (OEE) is a crucial metric for manufacturing efficiency. It encompasses three key performance indicators: Availability, Performance, and Quality. By measuring these components, you can pinpoint inefficiencies and take actionable steps to improve your processes, optimizing your production line.
The Foundation: Understanding the Components of OEE
OEE is calculated by multiplying the three components: Availability, Performance, and Quality. Let’s break down each component:
1. Availability
Availability is all about how often the equipment is ready for production. It’s calculated by dividing the actual production time by the planned production time.
- Example: Let’s say your machine was scheduled to run for 480 minutes (8 hours), and it only managed to run for 420 minutes due to breakdowns. Your availability would be 420 / 480 = 0.875 or 87.5%.
2.Performance
Performance measures whether the equipment is running at its maximum possible speed. It’s determined by dividing the ideal cycle time by the actual cycle time.
- Example: Your machine is capable of producing a widget every minute (ideal cycle time). If in reality, it’s producing a widget every 2 minutes, your performance is 1 / 2 = 0.5 or 50%.
3.Quality
Quality assesses the percentage of good parts produced versus the total parts produced. It’s calculated by dividing the number of quality products by the total number of products produced.
- Example: If you produced 1000 widgets but only 950 passed quality control, your quality rate is 950 / 1000 = 0.95 or 95%.
How to Calculate OEE
Now, let’s put it all together. To calculate OEE, multiply the availability, performance and quality percentages.
- Formula: OEE = Availability x Performance x Quality
- Example Calculation:
- Availability: 87.5%
- Performance: 50%
- Quality: 95%
- OEE = 0.875 x 0.5 x 0.95 = 0.415 or 41.5%
SIMPLE OEE Calculation Steps
Let’s break down the SIMPLE steps for OEE calculation:
- Record Planned Production Time: Document the total time that production is planned.
- Calculate Operating Time: Subtract any Downtime from the Planned Production Time.
- Measure Ideal Cycle Time: Determine the time it would take to produce one piece idealistically.
- Count Total Output: Record the number of pieces produced.
- Count Good Pieces: Record the number of quality pieces produced (excluding rejects).
- Calculate Availability, Performance, and Quality using the formulas provided.
- Multiply these three percentages to get your OEE score.
Improving Your OEE – Practical Tips
Improving OEE involves a systematic approach:
- Maintenance: Regular and preventive maintenance can minimize downtime.
- Training: Ensure operators are well-trained to handle equipment and troubleshoot common issues.
- Monitor: Use real-time monitoring tools to keep track of production metrics.
- Optimize: Streamline production processes and minimize non-value-added activities.
Common Pitfalls to Avoid in OEE Calculation
Neglecting certain factors can skew OEE calculations. Be mindful of:
- Unrecorded Downtime: Ensure all downtime is accounted for.
- Incorrect Cycle Time: Use realistic cycle times for performance measurement.
- Ignored Small Stops: These can accumulate and significantly impact performance.
Conclusion: Mastery Over OEE Calculation
Mastering OEE calculation means understanding its components, accurately capturing data, and continuously working on improvements. By following the Secret Formula for Perfect OEE Calculation Revealed! and utilizing the SIMPLE OEE Calculation method, you’ll be on your way to enhancing your operational efficiency.
Call to Action
Ready to boost your manufacturing efficiency? Start implementing these steps now and share your experiences with us. For more tips and insights, subscribe to our blog or contact us for personalized advice
OEE calculation very useful. Thanks
Great, Clearly understood.